Digital Twin & AI-based Control
CARLA is an open-source simulator for autonomous driving, enabling realistic simulations of city and highway environments. This thesis aims to develop a sustainable navigation system for electric vehicles to extend their lifespan and achieve ecological benefits. Tasks include designing a path planning algorithm in CARLA, integrated with MATLAB and Simulink, to minimize the lifetime consumption of Power MOSFETs. System integration will involve the virtual vehicle testbench, which provides an online lifetime consumption index. Additionally, customized test maps should be created using RoadRunner to simulate diverse conditions and validate the algorithm’s effectiveness.
Vorkentnisse:
- Courses: Completed RPSS1 and RPSS2 lecture series.
- Technical Skills: Experience with AI/ML/NN techniques;
proficiency with ROS2, RViz; strong foundation in Python,
MATLAB, and Simulink. - System Requirements: Familiarity with Ubuntu or other
Linux distributions.
Contact:
Contact
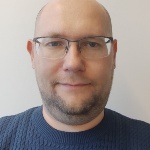
Oleksandr Solomakha
Dr.Research Assistant
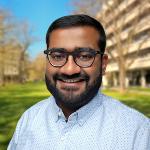
Swapnil Sunil Roge
M.Sc.Research Assistant