Im Zuge des vom BMWi geförderten Projektes „Innovative Prüfmethodik für Faserverbundbauteile im Rotorblattsektor “ kurz InFaRo wird ein Radarsystem zur Überprüfung von Rotorblättern von Windkraftanlagen entwickelt.
Die zerstörungsfreie Werkstoffprüfung ist ein wichtiger Bestandteil im Produktionsprozess von Rotorblättern für Windkraftanlagen. Hierfür stehen verschiedenste Systeme zur Verfügung. Die konventionellen, wie Thermographie oder Ultraschall, liefern schon heute gute Ergebnisse bei der Fehlererkennung. Radarsysteme jedoch bieten die Möglichkeit die Überprüfungen zu vereinfachen und weiter zu verbessern.
Durch den Entwurf eines H-Band-Radars kann die Auflösung im Vergleich zu bereits existierenden Systemen im W-Band erhöht und damit Fehler im Material besser erkannt werden. Dies führt zu einer erhöhten Qualität in der Herstellung, Vermeidung von Kosten durch ansonsten anfallende Wartungsarbeiten und natürlich auch zur Erhöhung der Sicherheit der Windkraftanlagen, da bestimmte Defekte konsequenter ausgeschlossen werden können.
Das Institut für Robuste Leistungshalbleitersysteme (ILH) hat den Entwurf der Sende- und Empfangskomponenten („analoges Frontend“) eines solchen H-Band-Radars als Schwerpunkt. Die breitbandigen Sender und Empfänger im hohen Millimeterwellenfrequenzbereich werden in Form von monolithisch integrierten Millimeterwellenschaltungen (MMIC) auf Basis der Halbleitertechnologie des Fraunhofer IAF entworfen, für die Spezifikationen des Projektes optimiert, und am Fraunhofer IAF im Rahmen von Multi-Projekt-Waferruns hergestellt.
Neben dem ILH setzt sich die Verbundstruktur noch zusammen aus dem Fraunhofer Institut für Angewandte Festkörperphysik (IAF) als Projektkoordinator, Composite Material Supply (CMS), die Materialproben liefern und das Messsystem während der Produktion von Windkraftgurten testen, Composcan, die Vergleichsmessungen mit Thermografie durchführen und das Messsystem aufbauen und der Gesellschaft zur Förderung angewandter Informatik (GFaI), die eine geeignete Softwarelösung für das Messsystem entwickeln, um die Messdaten sinnvoll zu visualisieren und auszuwerten.
Weiterführende Informationen unter:
www.infaro.de
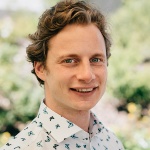
Christopher Grötsch
Dr.-Ing.Wissenschaftlicher Mitarbeiter